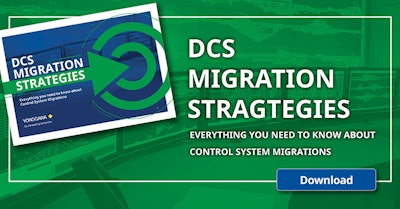
Everything you need to know about
Control System Migrations
INDEX
2
1
3
4
5
6
INTRODUCTION
UNDERSTANDING MIGRATION
CRITICAL MIGRATION CHOICES – FIRST STEPS
CRITICAL MIGRATION CHOICES
HOW CAN OUR SYSTEM BE BETTER?
MANAGING A MIGRATION
REALIZING THE BENEFITS
CHAPTER 01
INTRODUCTION
4WHAT’S CONTROLLING
YOUR PLANT?
A process manufacturing plant of any size and complexity usually has
thousands of field instruments, valves, operator interfaces and other
devices working together to make the process run efficiently and reliably.
All those parts are connected and controlled by the DCS—the distributed
control system, a complex collection of processors and input/output
systems capable of making everything work together. Smooth operation
of the DCS is absolutely necessary for your plant to operate efficiently.
In spite of its criticality, many companies have old DCS platforms. In
computing terms, they’re ancient. Various studies suggest the majority
of plants have systems more than 20 years old, and 30 year-old systems
are rather common. Some parts have been updated over the years, but
the basic core processors and much of the I/O hardware could easily date
back to the days of floppy disks. Those systems should have been updated
long ago.
READ MORE - CENTUM HISTORY
In 1975, Yokogawa launched CENTUM to introduce the world’s
first distributed control system (DCS). While Yokogawa’s corporate
philosophy remains unchanged, CENTUM has been making
progress and expanding its functions along with advances in
technology, environmental changes, and changing demands since
its release several years ago. CENTUM offers 42 years of progressive
compatibility.
Download this technical report to read about the history of the
first DCS and how it has evolved over time.
CHAPTER 1 | INTRODUCTION
THE WORLD’S 1ST DCS
5For many companies, the DCS is like the light in a kitchen. It’s up on
the ceiling and uses the same 100-watt incandescent bulb it’s had
forever. Yes, it’s inefficient—newer bulbs would give more light with
far less energy—but it works and so nobody does anything about
it. When it finally burns out someone will put in a better bulb, but
for now the homeowner simply continues to waste money and lives
with the existing substandard performance because making the
change is too much trouble.
Because the average lifecycle of a DCS is very long and the system
is likely to keep working, it is easy to maintain the “If it Ain’t Broke”
mentality and keep the old DCS running. But what if something
goes wrong?
IF IT AIN’T BROKE…
AUTOMATION SYSTEM COMPONENTS LIFECYCLE
The average lifecycle of most components of a process automation system is longer than
15 years. In many cases, systems are maintained by replacing individual components.
AU
TO
M
AT
IO
N
S
YS
TE
M
LIFECYCLE
20-50 YEARS10 YEARS5 YEARS
INDUSTRIAL
EQUIPMENT
(e.g. Network SW)
FIELD DEVICE
WINDOWS OS
COMPUTER
HARDWARE
EXPENDABLES
(e.g. Batteries)
CONTROL SYSTEM
PLANT
Staying on an antiquated platform may be preventing you
from realizing operational efficiency gains and streamlining
business decisions with clear information.
CHAPTER 1 | INTRODUCTION
6RISKS | WHAT JUST HAPPENED?
Many companies continue to keep old DCS platforms running, until they can’t.
Over time, electronic components degrade and fail. That’s when things get
exciting, but in a bad way. Old control system platforms and instrumentation
increase the risk of failure and production interruptions, and lack many of the
capabilities of newer systems for improving plant performance.
A TYPICAL DAY IN THE PLANT WITH AN OLD CONTROL SYSTEM
WE JUST LOST ALL THE TEMPERATURE READINGS
IN THE DISTILLATION COLUMN.
Why? An I/O card just failed and all the readings coming
in on that card went dark.
THE FLOW LOOP CONTROLLING FEEDBACK INTO
UNIT 3 WENT HAYWIRE.
Why? That part of the controller quit. Put it into manual or
see if you can rig up some other workaround.
WE HAD AN UPSET IN REACTOR B.
Why? The two variables critical to keeping the reaction balanced
are not visible on the same HMI screen. The operator has to toggle
back and forth and can’t see them side-by-side. It’s a throwback to
the original system design.
CHAPTER 1 | INTRODUCTION
7WHAT ARE YOUR RISKS?
Plant managers and operators often consider plant downtime as the major risk and
cost of using an older system, but in fact, plant downtime is only one of many risks
to consider. These are the top five risks and costs that are often associated with
outdated control systems:
CHAPTER 1 | INTRODUCTION
Roessler, D. (2013). Control System Migrations A Practical Project Management Handbook. New York: Monument Press.
System Failures Part Availability Difficulty Integrating New Applications & Systems Reduced Support Availability Operational Inefficiency
Result • Decreased Reliability
• Increased Downtime
• Extended Outages
• Lost System Functionality
• Increased Maintenance
Requirements
• Can’t Realize Full Potential of
New Application
• Key Data Not Easily Available to
Decision Makers
• Difficulty Trouble Shooting
Maintenance Issues
• Extended Schedules for Projects
Requiring Engineering
• Inability to Take Advantage of
Current Best Practices
• Operator Mistakes Contributing
to Product Quality Issues and
Downtime
Costs • Lost Production
• Unplanned Outages
• Product Schedule & Shipment
Disruptions
• Increased Maintenance Costs
• Lost Production
• Impact to Production Quality
• Less Optimized Operational
Performance
• Slower Business Decisions
• Higher Costs Associated with
Project Implementations and
Ongoing Support
• Increased Maintenance Costs
• Increased Engineering Costs
• Delays in Realizing Benefits of
Projects Involving Control System
Configuration
• Reduced Product Quality
• Increased Downtime
• Operator Stress
!
8HOW MUCH RISK IS TOO MUCH?
If you’ve ever encountered a crisis in your plant, you’re not alone. Maybe the situation
wasn’t too extreme. Maybe you were able to find an old processor card, but how long will
it last? How much time until you go through this crisis again, but without a spare? When
will you get to the point of no return?
As the frequency of these events increases, so do the risks associated in maintaining the
system. It’s important to complete an analysis of the system risks and benefits to see at
what point the risk of doing nothing exceeds the risk of doing a migration.
An unreliable DCS means an unreliable plant. If a plant can’t produce, it doesn’t make
any money. Such events cause high-level people to ask what has to happen to prevent
such outages.
The answer is simple: Look into your DCS capabilities and find out what may be improved.
CHAPTER 1 | INTRODUCTION
Color Status Comment
Healthy No issues detected - no action required
Attention Some issues have been detected - action may be required
Critical Critical issues have been detected - immediate action is required
N/A Not available / not applicable
Category Comment Status
System Overview Overview of system compnents
Hardware Lifecycle Phase and HW status
Software Lifecycle Phase Lifecycle Phase and SW status
Operating System Lifecycle Phase
Alarm Rate EMUA 191 and ISA 18.2
Control Mode Time in normal mode vs. off mode
Production KPIs met
Operating KPIs met
System Traffic Rating Throughput per segment
Network/Cyber Security Rating Completely islanded and proprietary system
Node Memory Usage
Node CPU Processing Rating
The image on the left represents a “System Health Check,” which is a service offered to
Yokogawa DCS customers.
CHAPTER 02
UNDERSTANDING MIGRATION
10
WHAT IS MIGRATION?
CHAPTER 2 | UNDERSTANDING MIGRATION
The word migration implies large-scale movement and change.
The concept applies when talking about changing to a new DCS
platform because these are not small systems. They are complex
and launching such a project is not a trivial matter, which is one
of the reasons some companies try to keep their old systems
running for so long.
A DCS migration is a project where some or all of your
automation control equipment gets replaced. Just as no two
systems are exactly alike, neither are two migration projects.
A DCS COMPRISES SEVERAL MAIN SECTIONS:
I/O
CENTRAL
CONTROLLERS
INTERNAL
NETWORKING HMIs
DCS
FIELD
WIRING AND
MARSHALLING
Copyright © 2016 Yokogawa Corporation of America
11
POSITIVE ASPECTS OF MIGRATION
CHAPTER 2 | UNDERSTANDING MIGRATION
To a plant struggling to keep the DCS up and running, a migration is largely a defensive measure. It is driven
by an urgent necessity, but there are still opportunities to realize many of the technological advances of the
last few decades. Others may know their system is old and its days are numbered, but there is still time to
make a rational decision and launch a well-planned migration before things fall apart.
The DCS you install today may never have to be completely replaced because its modularity will allow it to be
improved incrementally.
New systems are highly adaptable, built on more open platforms, and are more flexible than those from just a
few years ago. In addition to avoiding unplanned shutdowns, a migration offers some additional benefits:
Greatly improved price/performance ratios Easier to integrate with enterprise systems Better self-diagnostic capabilities
More modular and built on open platforms More sophisticated HMIs Less dependent on specialized hardware
Improved networking and interconnectivity Stronger cyber security Improve operational performance and decision making
Network-IO (N-IO) offers both hardware-
based flexibility and software-based
configurability
Able to integrate more thoroughly with
safety systems Able to interface with smart field devices
12
HOW MUCH MUST WE CHANGE?
CHAPTER 2 | UNDERSTANDING MIGRATION
Once you have identified opportunities for improving your DCS
capabilities, it is now time to choose an approach in getting there.
Consider the following options:
OPTION #1: RIP & REPLACE
Companies facing serious system failures have little choice but to
replace their DCS. When simply keeping the plant running is a struggle,
it’s time for migration.
OPTION #2: STEPWISE MIGRATION
For less drastic situations, there are two basic approaches:
1ST APPROACH: Start in the control room and begin by improving
the HMI
Primarily driven by functional improvements—we want better
visibility for running the process, and more connectivity to integrate
with other plant systems.
2ND APPROACH: Start with the controllers.
Primarily driven by reliability considerations—our controllers are
failing too frequently and interrupting production
OPTION #3: I/O
The I/O is somewhere in the middle and may be part of either approach.
The existing I/O may be compatible with the new controllers and not
require replacement, or the migration may entail replacement of the I/O.
In either case, the actual field instruments are usually left in place unless
they are also quite old and subject to frequent failures. Field wiring from
the I/O to the field devices also typically stays unless it is in very bad shape.
Replacing wiring in an existing plant is hugely expensive.
CHAPTER 03
CRITICAL MIGRATION CHOICES
FIRST STEPS
14
Arguably the most important people to include are the operators. They will work with
the new system more than anybody else. They also know the most about the existing
system including its strengths and weaknesses. Other areas engage with the system at
various levels and should certainly participate. Some functional areas not listed above
are tangential and may not need a member on the team, but should offer suggestions
and follow the progress. Ultimately the new solution should reflect the needs of as many
stakeholders as possible.
FORMING AN INTERNAL TEAM
CHAPTER 3 | CRITICAL MIGRATION CHOICES – FIRST STEPS
The first step of a DCS migration is forming an internal team to oversee the effort. Teams are good because they ensure viewpoints
from different areas are heard, create a natural mechanism to spread out the work, and create widespread buy-in for the new system.
PLANT MANAGMENT/
CAPITAL BUDGET
Capital budget, safe plant operations,
meet production goals, meet
regulatory requirements, retain
knowledge and expertise as the baby
boomers retire, struggle to do more
with less
OPERATORS/OPERATIONS
Responsible for the operation of
the facilities in the control room
and to identify and communicate
issues with other members of
the team to ensure maximum
production quantity and quality
ENGINEERING
Plant turn-arounds, engineering
costs, process design, control
strategies, system architecture,
goals, improve staff productivity,
standard operating procedures
MAINTENANCE
Perform scheduled and
unscheduled maintenance on
control room equipment as
directed by the lead engineer
15
DEFINING SCOPE & CHOOSING
A VENDOR/PARTNER
CHAPTER 3 | CRITICAL MIGRATION CHOICES – FIRST STEPS
Once a project has been launched and the team formed, the direction turns more specific
and technical. Two things happen early in the process, and they should overlap somewhat
because they influence each other:
Defining the project’s scope and specifics
Choosing a vendor/partner
Start with the scope because it will influence vendor selection, but the vendor will also
influence the scope. Vendors will approach the project in the different ways. Some will
provide extensive assistance with implementation, while others may simply deliver the
hardware and software and expect others to do the site work. This results in very different
project experiences, so consider the pros and cons of each.
Few companies choose a 100% DIY path for a control system. It might be possible for a
small unit, but a plant of any size will need to partner with a DCS vendor, typically making a
selection from a list of several candidates. Since the lifespan of most major control systems
is measured in decades, the choice of a partner is an important decision.
Going back 20 or 30 years, there were more system choices, and the differences between
vendors were more pronounced. Since then, several older platforms were absorbed into
larger product lines and then phased out by new vendor owners. In those cases, the
vendor will guide users to consider newer platforms.
Several companies still operating under their original name have also phased out their old
platforms. Once MS Windows-based systems emerged in the 1990s, architectures changed
significantly from the older proprietary systems, even within a given system vendor.
Consequently, there is sometimes little reason to remain with the same vendor company.
16
CONSIDER A MAIN
AUTOMATION CONTRACTOR
CHAPTER 3 | CRITICAL MIGRATION CHOICES – FIRST STEPS
DO IT YOURSELF OR PARTNER UP?
The ability to deliver the full scope of project execution in industrial
automation projects is more important than ever. However, companies
are increasingly constrained by personnel issues, budgets, and shrinking
timetables. Companies are also faced with the task of executing multiple
projects simultaneously in disparate geographic regions.
The Main Automation Contractor (MAC) owns responsibility over the
entire automation related aspects of the project. Many of the world’s
leading end users are applying the MAC approach to their entire capital
project. The MAC approach can result in project cost savings up to 30%
against a traditional approach.
BENEFITS OF THE MAC APPROACH
Reduced project risk
Total project management
Commitment to the customer on
a corporate level
Automation standardization for
multi-projects
Shortened delivery times
Global engineering locations
and resources
Reduced customer management load
Single point of responsibility and
single window
Entire automation design and
engineering
Design of automation standards
Reduce customer oversight
management during execution
Cost savings by dealing with
vendor directly
More efficient and consistent
engineering using a global
engineering resource pool
17
IDENTIFYING A VENDOR:
NARROWING THE FIELD
CHAPTER 3 | CRITICAL MIGRATION CHOICES – FIRST STEPS
In most situations, by asking a set of basic questions, it is relatively easy
to split off at least half of the possible candidates and narrow the range
down to two or three candidates, like the finalists in a beauty pageant.
The checklist on the right provides practical guidance for your
evaluation process.
The last question might be the hardest to answer, but most vendors will
say, “yes” based on experience. “System X has been used successfully
in these applications and users are very happy with its capabilities, so
it can certainly run your plant.” Such an answer may be correct and
relevant provided the vendor can cite examples meaningful to your
company, and provided plant personnel check out references in detail
via phone calls, or even plant visits if possible. There is no benefit in
being your vendor’s first venture into a new industry.
Specify process control requirements: What does your plant do, and what basic
control capabilities are necessary to keep it operating effectively.
Specify HMI requirements: Is a drive to have high-performance HMIs on the list?
Walk around control?
Specify performance capabilities: What availability rate do you expect from the
system?
Specify platform capabilities: How easy is it to add specific functions such as
APC strategies? How easy is it to scale up to a larger process unit?
Evaluate the installed base in your specific industry: How many plants like
yours are using this platform? Consider the specific manufacturing process along
with size.
Evaluate compatibility with the parts of your system that will remain in
place: Few migrations are total, so will the elements retained integrate easily with
the new DCS?
Evaluate compatibility with your intellectual property and control strategy:
How easy will it be to transfer the intellectual property contained in your control
code?
Consider accumulated experience of plant personnel: Do you have people in
your plant with experience on a given platform from elsewhere?
Is your system Future Proofed? Does the system have a proven track record
and plan that allows it to be upgraded in place with mixed components?
(i.e. does it provide progressive compatibility that allows you to just upgrade the
components you need without your entire system and production?)
Can the system do what you need for your process? Is it possible to know for
certain?
EVALUATION CHECKLIST
FUTURE PROOF
A helpful approach is to allow customers to “progressively upgrade in place” and not
force a rip and replace. This allows for smoother upgrades without forcing an intra-
system “migration.” Customers can easily incorporate the latest operating technology
into their system and reap the efficiency gains of a modern control system (which is part
of their critical business infrastructure).
18
EVOLUTION OF YOKOGAWA
CONTROL SYSTEMS
CHAPTER 3 | CRITICAL MIGRATION CHOICES – FIRST STEPS
F-Bus
250 KBPS
Dual
Redundant
Token Pass
HF-Bus
1MBPS
Dual
Redundant
Token Pass
V net
10 MBPS
Dual
Redundant
Token Pass
CFCS CFCD
CPOS
1975
CENTUM
1983
CENTUM V
CFCS2
COPS2
COPSV
CFFS
1988
CENTUM-XL
CFCS EFCD
EOPS ENGS
1993
CENTUM CS
EWS ICS
1998
CENTUM CS 3000
HIS ENG
LFCS KFCS
2001 2005
CENTUM CS 3000 R3
2008
CENTUM VP
2011
CENTUM VP R5
New
FFCS
HIS
HIS
AVR
CFCD2
ABC
PICS
FFCS-L
V net I/P
1Gbps
Dual
Redundant
PFCS
FFCS-V
ENG
2014 -
CENTUM Offers 42 Years of Progressive Compatibility
Yokogawa has paid particular attention to helping its customers manage lifecycle
costs by optimizing the upgrade process. All of Yokogawa’s legacy CENTUM systems
can be controlled and monitored from a newer CENTUM system. By allowing its
customers to utilize their existing assets wherever possible, Yokogawa offers them
a cost-effective way to upgrade their production control systems.
CHAPTER 04
CRITICAL MIGRATION CHOICES
HOW CAN OUR SYSTEM BE BETTER
UNDERSTANDING THE POSSIBILITIES
CHAPTER 4 | CRITICAL MIGRATION CHOICES – HOW CAN OUR SYSTEM BE BETTER
When a company running an old DCS considers something new, the team
is often left struggling to get a sense of what’s available with current
technologies. If you haven’t looked at cell phones since 1995, you’ll be hard
pressed to imagine what they can do now.
Certainly the new system must do what the old one did, but beyond those
functions, it’s difficult to project. Some companies simply stop there: “Give us
the same thing, but on a newer and more reliable platform.” Such thinking can
turn into a huge lost opportunity if the company doesn’t make a serious effort
to embrace all the available improvements.
High performance HMI
Improve production throughput
Improved APC integration
Improved alarm management
System security
Efficiency with function block library
Reduced system maintenance cost
Reduced production cost
Improve situation awareness
Support “aging in place”
Decision support for business
and plant operation
Reduced safety
incidence
Improve production
quality
Capture intelligence within
configurable system
OBVIOUS VS. HIDDEN BENEFITS
OF MIGRATING TO A NEW DCS
20 Copyright © 2016 Yokogawa Corporation of America
It is important to do the homework of determining what you might want and what’s available,
as this will make for better discussions with vendors as you start to get into specifics.
21
SPECIFYING STRATEGIC
OPERATIONAL CAPABILITIES
Part of defining the scope is specifying what you want from your new system
and discussing specific points with your short list of vendors. Here are some
general ideas worth exploring:
More
sophisticated
networking
capabilities:
These extend
connectivity
to enterprise-
level systems,
but also permit
implementation of
modern technologies
such as remote
access, walk-around
control and wireless
field devices.
Greater reliability:
Today’s platforms
are generally more
stable and reliable
than older systems,
some particularly so.
More sophisticated
control strategies:
Many tools are
available to help
improve control
performance, such as
loop diagnostics and
process optimization.
Improved APC:
Extending beyond
traditional regulatory
control allows for
new techniques
tuned to specific
manufacturing
processes.
Alarm
rationalization and
management:
More thorough alarm
rationalization and
analysis can make life
easier for operators
and help avoid alarm
floods, nuisance trips
and downtime.
Improved HMIs:
Better strategies
built around the
ways operators
do their jobs
improve situational
awareness, while
better graphics avoid
fatigue during long
shifts.
Modular procedural
automation:
Automating steps
for procedures help
capture operator
knowledge and
implement best
practices to avoid
incidents during
transition times.
Future Proof:
DCS migrations
or upgrades can
be costly and time
consuming. Consider
how future upgrades
can or will take place.
Consider platforms
that will allow you to
update at your own
pace, without system
shutdowns, and will
support mixing node
releases.
1 2 3 4 5 6 7 8
CHAPTER 4 | CRITICAL MIGRATION CHOICES – HOW CAN OUR SYSTEM BE BETTER
22
SPECIFYING CAPABILITIES:
SAFE NETWORKING
A DCS designed decades ago had one purpose: control the process. It did its
job in isolation. However, as enterprise-level management demanded more
detailed production data, connections were made to upper level systems to
transfer information back and forth. Naturally, these communication demands
put stress on the networks, and sometimes created paths for cyber attacks.
Overnight, security became a major concern.
A DCS today has the required secure connectivity built in to make it part
of a much larger company ecosystem integrated with historians, asset
management platforms, ERP systems and others. Even real-time remote access
is now commonplace through the Internet. Every option might not appeal to
every user, but having such capabilities from the outset is better than trying to
add it later.
CHAPTER 4 | CRITICAL MIGRATION CHOICES – HOW CAN OUR SYSTEM BE BETTER
23
Remaining secure requires the
installation of a continuous flow of
new security patches, which contain
software fixes for vulnerabilities.
Vendors of operating systems have a
limited support window for security
fixes; once the product is no longer
sold, the support is generally limited to
a three-to-five-year period. After this
period, no more security patches will
become available, resulting in a rapid
degradation of the product’s security.
Software that protects the process
control system, such as anti-virus and
whitelisting applications, also has
support limitations pertaining to legacy
platforms. Therefore, legacy systems
can suffer from the unavailability
of security patches as well as the
unavailability of security protection
software.
SPECIFYING CAPABILITIES:
SAFE NETWORKING
VULNERABLE EQUIPMENT
The continuous evolution of the control system enables organizations to
protect the investment in equipment and control strategies over long periods
of time. However, interfacing decades-old controllers with current technology
also makes this equipment indirectly vulnerable to attack.
HOW DOES THIS AFFECT SECURITY?
Old control systems may experience gaps in
support, which makes them more vulnerable
than contemporary systems.
CHAPTER 4 | CRITICAL MIGRATION CHOICES – HOW CAN OUR SYSTEM BE BETTER
24
SPECIFYING CAPABILITIES: RELIABILITY
A DCS platform has to run reliably, without interruption, 24/7/365 for years at
a time. If the DCS hiccups, the process can shut down, piling up costs made
worse by lost revenue. Through use of sophisticated code writing combined
with strategic redundancies, leading DCS vendors have built exceptionally
stable systems capable of seven nines reliability, with 99.99999% uptime.
THE VALUE OF SEVEN 9s SYSTEM AVAILABILITY
ESTIMATED YEARLY
DOWNTIME
(1 FCS)
ESTIMATED YEARLY
DOWNTIME
(10 FCS)
ESTIMATED COST
DAMAGE
(10 FCS)
MTBF
(10 FCS)
FAILURE
COUNT
12 YR
SYSTEM
SHUTDOWN COST
12 YR
COST
DAMAGE
12 YR
SEVEN-9
(99.99999%) 3 Sec 31 Sec $2.5 Thousand 450 years Negligible Negligible Negligible
FOUR-9
(99.99%) 0.86 hrs 8.6 hrs
$2.5 Million 0.4 years 24 4 times
more than $85
Million
The seven nines reliability numbers have been verified in tests and actual system performance at
installed plant sites, and their value is illustrated in this chart.
CHAPTER 4 | CRITICAL MIGRATION CHOICES – HOW CAN OUR SYSTEM BE BETTER
25
SPECIFYING CAPABILITIES:
RELIABILITY
CHAPTER 4 | CRITICAL MIGRATION CHOICES – HOW CAN OUR SYSTEM BE BETTER
Having a system that is reliably up and running is critical not only for production, but also
for brand management, safety to employees, safeguarding the environment and protecting
your overall investment (in terms of time, knowledge and equipment). Studies of industrial
accidents show that one of the largest contributing factors to an incident is human
error. Furthermore, these errors occur at a higher rate when the process is undergoing
a transition or rare operating condition such as start-up, shutdown, or upset event with
attempted recovery. This is why having a system with seven nines reliability is so important.
A five-minute event that requires operator intervention creates an environment of higher
risk. Choosing your risk tolerance and supporting that decision with a system that delivers
reliability and quality service is critical to your operations.
BP American Refinery Explosion, Texas City, March 2005
“A disproportionate percentage of process safety incidents have occurred during
transient operations, which include those conducted infrequently such as startups
or shutdowns as well as abnormal or emergency events. A typical refining or
petrochemical facility will spend less than 10% of its time in transient operations –
yet 50% of process safety incidents occurred during these operations.”
Chemical Processing Magazine, 2010
26
80
80
100
100
Optimization
Multi-variable
Control (MVC)
Enhanced Regulatory Control (ERC)
Basic Control
100%
80%
30%
15%
60
60
40
40
20
20
0
0
CAPITAL COST (INCLUDING MANPOWER) (%)
BE
N
EF
IT
P
O
TE
N
TI
A
L
(%
)
A
D
VA
N
CE
D
P
RO
CE
SS
CO
N
TR
O
L
(A
PC
)
Typical APC Implementation Schedule
Multi-Variable Control (MVC) is the key component of an APC system, that enables optimum process stabilization,
resulting in increased productivity. MVC achieves this by predictive control using process dynamic models, which is
proving to increase throughput, save energy, and reduce quality giveaway.
SPECIFYING CAPABILITIES:
CONTROL STRATEGIES AND APC
APC capabilities have been around for a long time and many
sophisticated plants have used them to great advantage, even with
the old control system platforms. But users had to work hard because
designing APC systems required custom code writing, or bolting on
an external solution. New control systems have many built-in tools
available to support a variety of APC strategies without the need to
write custom code, making implementation far simpler.
Some of these process optimization approaches use “big data”
concepts, performing deep statistical analysis on historical process
data, looking for correlations to support improvements. The
networking capability of today’s systems makes this practical and
even easy to perform using a variety of built-in tools.
In addition to fast ROI, advanced systems provide many advantages
for the process units, such as:
Improved process yields
Increased throughput
Reduced energy consumption
Improved process stability
CHAPTER 4 | CRITICAL MIGRATION CHOICES – HOW CAN OUR SYSTEM BE BETTER
27
SPECIFYING CAPABILITIES:
CONTROL STRATEGIES AND APC
Ethylene
2-4% increase in production
VCM
3-5% increased capacity / 1-4%
yield improvement
Aromatics (50KBPD)
$3.4M-$5.3M
Ammonia
2-4% increased capacity / 2-5% less
energy/ton
Polyolefin
2-5% increase production / up to
30% faster grade transition
Upstream
1-5% increase in production
Cogeneration/Power systems
2-5% decrease in operating costs
Bleaching
10-20% reduction in chemical usage
Thermo Mechanical Pulping
$1M-$2M
APC RETURN ON INVESTMENT (BENEFITS/YEAR)
PETROCHEMICALS OIL & GAS INDUSTRIAL UTILITIES PULPINGCHEMICALS
CHAPTER 4 | CRITICAL MIGRATION CHOICES – HOW CAN OUR SYSTEM BE BETTER
28
ALARM MANAGEMENT BENEFITS
â–ş alarms, workload,
â–ş operator uncertainty,
â–ş operator errors,
operator response time
â–ş Identifying nuisance
alarms
â–ş Sequence of events
aids decision making
â–ş Integrated management of
change and rationalization
process
â–ş Tighter control of approval
workflows
â–ş Enterprise deployment and
access
â–ş No more unaudited
setpoint changes
â–ş Suppressed and disabled
alarms are reported
â–ş Automated notification to
relevant stakeholders
OVERALL
REDUCTION IN:
ENHANCES OPERATOR
RESPONSE THROUGH
SUPPORTS A STRUCTURED
APPROACH TO ALARM
MANAGEMENT THROUGH
PROVIDES A MECHANISM
FOR CHANGE CONTROL
SPECIFYING CAPABILITIES:
ALARM MANAGEMENT
A migration project is also a good time to perform a thorough alarm
management analysis. Plant operators are often faced with a high
number of alarms and abnormal situations. They are therefore
unable to respond quickly enough to prevent safety related incidents,
environmental issues, shutdowns and equipment damage. In
addition, a poorly applied alarm management philosophy may result
in excessive alarms that can cause operators to routinely ignore these
alarms due to the information overload.
Current DCS platforms have sophisticated alarm-processing
capabilities, but this does not reduce the importance of performing a
thorough hazard analysis and alarm rationalization project. This part
of the process depends on human analysis to create a system capable
of protecting the plant while avoiding nuisance alarms and floods,
and potentially devastating incidents and outages.
CHAPTER 4 | CRITICAL MIGRATION CHOICES – HOW CAN OUR SYSTEM BE BETTER
29
SPECIFYING CAPABILITIES:
IMPROVED HMIs
Studies exploring how operators do their jobs and interact with HMIs proved that early HMI design
techniques lead to operator fatigue and operator confusion during process upsets. The result of these
studies has been an improvement in situational awareness, allowing operators to understand what’s
happening in the process more quickly and accurately, and showing them how to react.
Implementing high-performance HMIs is not an automated process. Studying how operators work and
designing the graphics and screens to support them is a significant undertaking. There are advantages to
doing it during the migration project, but it can be done later on provided the new platform has the required
basic capabilities.
With old DCS platforms, the basic approach to an HMI was drawing a PID and inserting process variables
around the screens with a heavy use of colored text, lines, and objects on a black background.
Old HMI vs New HMI
CHAPTER 4 | CRITICAL MIGRATION CHOICES – HOW CAN OUR SYSTEM BE BETTER
30
SPECIFYING CAPABILITIES: MODULAR
PROCEDURAL AUTOMATION
Modular procedural automation (MPA) is a method to deal with
changes in the workforce, and to improve operations in general.
As baby-boomer workers retire and are replaced by
inexperienced millennials, tribal knowledge is being lost.
Companies realize this most clearly during start ups, shutdowns
or when making major process changes. These abnormal
situations don’t happen frequently, and they depend on the
ability of experienced operators to carry them off correctly.
When executing these abnormal procedures, plants are at their
most vulnerable.
MPA provides a mechanism to capture tribal knowledge and
bake it into the automation. The procedure used by the most
skilled operators can be documented and written into the
automated process, so when it is time to start up the plant or
perform some other abnormal operation, it’s as if the best
operator is there at the controls, and it’s done the same way
every time. MPC implementation isn’t practical on many older
DCS platforms.
The remaining skilled operators can also run larger sections of
the plant because the greater sophistication possible with a new
DCS expands a given individual’s span of control. One person
can watch and control more loops and units because the control
system does more of the work, and because of other DCS
improvements such as automated process optimization.
MODULAR PROCEDURAL
AUTOMATION EBOOK
Download this eBook and learn how to
enhance production and safety through
modular procedural automation
FREE YOKOGAWA EBOOK!
• Capture the best procedure from all
operator inputs
• Combine into a best practice procedure
CHAPTER 4 | CRITICAL MIGRATION CHOICES – HOW CAN OUR SYSTEM BE BETTER
31
FUTURE PROOFING:
PROTECT YOUR INVESTMENT
Equally as important as selecting a system is considering how to protect your
investment. Intellectual property and know-how is stored in the DCS in how it is
configured to run your process. You need a platform that can be updated over
time, allowing you to take advantage of new technology and other benefits like
improved safety and efficient operations. You should also look for a system that
allows you to update at your own pace and fully supports mixing node releases in
a single system without forcing a full update all at once.
For example, you may have a historian, advanced alarm management, safety
management, operator training simulator, or other advanced solution nodes.
When selecting a system, consider solutions that do not require you to upgrade
all of these advanced nodes at once, but instead allow you to upgrade only your
DCS system to a future version.
Known as “Future Proofing,” this process provides a path forward without ripping
out and replacing nodes and having to manually re-write code and re-configure
the control strategies. Future proofing protects the customer’s investment and
allows them to better manage cost – no need to conduct a major capital project
just to benefit from a few high value features. At the same time, the customer
knows they have a path to the future and can always keep their system “fresh.”
CHAPTER 4 | CRITICAL MIGRATION CHOICES – HOW CAN OUR SYSTEM BE BETTER
CHAPTER 05
MANAGING A MIGRATION
33
COMPRESSING THE PROJECT SCHEDULE
CHAPTER 5 | MANAGING A MIGRATION
The traditional approach for a migration or other large automation project is to lay out the steps in
a linear fashion on a timeline. When step two is finished, step three begins and when the last step
is done, everything gets tested. This approach works, but it takes a long time and allows problems
created early in the process to remain undiscovered until much later. With more aggressive
project management, it is possible to break up the linear timeline and have multiple steps occur
simultaneously. Steps two, three and four can overlap—with each part tested as it’s completed.
The main benefit is having the plant back in full production with its new DCS sooner, so financial
gains begin more quickly. This project management methodology is often referred to as Agile
Project Management, and it is becoming a common element of migration projects.
A new approach to Industrial
Automation Project Execution
Agile Project Execution
AGILE PROJECT
EXECUTION EBOOK
Download this eBook and learn how
to decrease industrial automation
project times
FREE YOKOGAWA EBOOK
Such an approach shortens the timeline significantly,
but it demands greater resources at critical times.
CHAPTER 06
REALIZING THE BENEFITS
35
COMPANY-WIDE IMPROVEMENTS
CHAPTER 6 | REALIZING THE BENEFITS
Improvements of the new DCS are not limited to the plant and control room. There will be many
valuable but less obvious effects and benefits felt throughout the company. Use this worksheet to
identify the places where you can find cost savings.
With fewer hardware failures, maintenance
can turns its efforts toward designing
new condition-based approaches using
diagnostic information from field devices
and other equipment.
Cost Savings: _______________
As uptime increases, schedulers can design
more efficient production programs.
Cost Savings: _______________
As many old operating systems are
eliminated with the old hardware, network
and other software maintenance becomes
far simpler.
Cost Savings: _______________
More secure networks allowing users
to extend remote access with greater
confidence.
Cost Savings: _______________
Spare parts inventory can be
reduced because failures are
much less frequent.
Cost Savings: _______________
STORAGE
CONTROL ROOM
36
Owners of Honeywell systems can certainly stay with the company and select an
appropriate migration strategy from those available. However, many of those
users have chosen to move to Yokogawa for a variety of reasons. CENTUM and
Yokogawa’s methodology offer many ways to improve operational excellence
while minimizing the cost of migrating to a new DCS platform. While users
considering a migration project might get caught up in technical details, it is
important to keep sight of the potential improvements possible with a newer and
better DCS.
Yokogawa’s system design, project execution methodologies, and track record delivers
the most reliable, lowest risk solution. Since introducing the world’s first DCS in 1975,
Yokogawa has helped thousands of migration projects, offering expert consulting and
flexible services to meet unique customer requirements.
Yokogawa has a migration solution and methodology that can help you safely and
efficiently move up from your existing process control system to our latest CENTUM
series production control system that has Future-Proofing built into the design. This
will help maximize operational excellence and give you a competitive edge over the
entire lifecycle of your plant facilities.
Yokogawa’s capabilities are well proven: Look no further than the thousands of
brownfield projects where we have migrated third party systems to a Yokogawa
process control solution.
WORKING WITH YOKOGAWA
Yokogawa works with you in the following ways to ensure a safe,
cost-effective and value-added migration process:
Assessing risk and advising on how to best address them
Optimizing existing assets
Maintaining quality
Minimizing production loss
Providing long-term support
YOKOGAWA DCS MIGRATIONS
CHAPTER 6 | REALIZING THE BENEFITS
READ MORE - MIGRATION METHODOLOGY
WHY YOKOGAWA?
37
Is your DCS meeting your production, operational, and risk targets?
Contact Yokogawa for a DCS Health Check and Migration assessment
where we’ll cover:
DCS Release and Support within its Lifecycle
Alarm Management Practice and Philosophy
Alarm Rates
Alarm: Operator Action Ratio
OS Release and associated Security Risk
Process Operator Graphic Design Performance Assessment
Loop Mode and Manual Changes
Procedure Use Assessment
REQUEST A DCS HEALTH CHECK AND MIGRATION ASSESMENT
GET MORE OUT YOUR DCS SYSTEM
CHAPTER 6 | REALIZING THE BENEFITS
Time
Conventional Investment Pattern and System Performance
Cost
Performance
Time
New Approach:
Progressive Compatibility and Lifecycle Performance Care Service
Cost
Performance
MODULAR
PROCEDURAL
AUTOMATION
Download this eBook and
learn how to identify MPA
opportunities at your plant.
DOWNLOAD
Download this eBook and learn
how to plan for and achieve a
successful project.
DOWNLOAD
UPDATE, UPGRADE,
MIGRATE OR REPLACE
OTHER PUBLICATIONS
Download this eBook and
learn why conventional project
execution no longer works.
DOWNLOAD
AGILE PROJECT
EXECUTION EBOOK
Download this eBook and learn
how to efficiently and safely
manage combustion.
DOWNLOAD
COMBUSTION &
FIRED HEATERS
Copyright © 2017 Yokogawa Corporation of America
A B O U T Y O K O G A W A
Yokogawa’s global network of 114 companies spans 59 countries. Founded
in 1915, the US $3.7 billion company conducts cutting-edge research and
innovation. Yokogawa is engaged in the industrial automation and control (IA),
test and measurement, and other business segments.