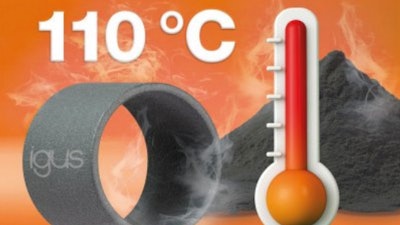
igus announced its new iglide i230 3D printing material for selective laser sintering (SLS). This new powder material can withstand temperatures up to 110°C, expanding the use cases for SLS-printed polymer components.
During SLS, a printer melts plastic powder layer by layer to form bearings and other components. However, parts made from standard SLS printing materials such as PA (nylon) 12 are generally limited to applications less than 80°C. Higher temperatures cause the material to become soft and lose dimensional stability, preventing SLS-printed components from being used in applications like automotive engines.
"As the demand for 3D-printed plain bearings for applications with high ambient temperatures has increased, we have developed a new SLS printing material called iglide i230," says Paul Gomer, 3D Printing Material Developer at igus.
Tests performed according to DIN EN ISO 75 HDT-A and HDT-B have demonstrated iglide i230's heat resistance. Printed parts made from the material do not deform at 80°C. They can withstand long-term exposure to temperatures of 110°C and even short-term exposure to 170°C without deforming.
"3D-printed plain bearings made from iglide i230 have a significantly longer service life, increase the efficiency of machines, systems and vehicles and reduce the need for maintenance," says Gomer.
At the same time, iglide i230 offers 50-percent more mechanical strength than PA 12 at room temperature. "This makes it possible, for example, to achieve the same component strength in plain bearings with a thinner wall thickness and to save room and weight in compact installation spaces," emphasises Gomer.
Other features of iglide i230 include:
- Free of polytetrafluoroethylene (PTFE).
- Roughly 80-percent more wear-resistant than PA 12.
- Has withstood pressures of 94 MPa during bending tests.
- Protects machines and systems from electrostatic discharge.
- Does not require time-consuming relubrication work, as solid lubricants are integrated into the material to ensure low-friction, dry operation.